Production of simple or complex parts, in small to large series
GMI demonstrates its technical expertise in shaping plastics by thermoforming by offering a complete, overall solution.
Its industrial process guarantees conformity of parts, safeguards deadlines and optimises productivity.
In combination with other technologies in which the Group has expertise ( welding, rotomoulding or polyurethane), GMI is able to deliver entire projects.
Design office
Equipped with the latest software packages for CAD data processing (CATIA V4 / V5, Solidworks software…), the design office provides flexible, responsive support for all your thermoforming projects.

Thermoforming tools
Working directly with the design office, the Tools division creates the thermoforming moulds (CADM).
These moulds are generally made:
— In medium or machinable board mainly used for prototyping
— In stratified resin or monobloc
— In machined aluminium
— Modular tools
— Tools with movable elements
— Regulated tools
The Tools department is responsible for managing moulds and draws up the maintenance plans for recommencing production at a later stage. Tools that are not being used in production are stored in a secure site.
Thermoforming machines
We are able to accept all projects thanks to a comprehensive fleet of machines.
Large-scale automatic and semi-automatic thermoforming machines are able to produce simple or technical parts measuring 2700 x 1800 mm/ Max forming height 750 mm.
Our latest acquisition is an XXL thermoforming machine capable of producing exceptionally large plastic parts:
3.50 m long x 2.50 m wide x 1 m deep, giving a plastic part with a surface area of 8.5 m2.
As a result, our customers benefit from reduced assembly costs and an optimised design in a single piece. And as a reminder, these large-format industrial parts are made from 100% recyclable thermoplastics.
Whether for sectors as varied as agriculture, special vehicles, boating, medical, design or railways, GMI has the capacity to produce the following XXL plastic parts:
– Bumpers for special vehicles
– Bodywork, roofs and interior fittings for agricultural or public works machinery
– Swimming pool components (stairs, etc)
– Boat covers
– Leisure pools
– Bathtubs
– Walls and interior linings for motorhomes, vans and campers
– Custom signs
– And so much more!
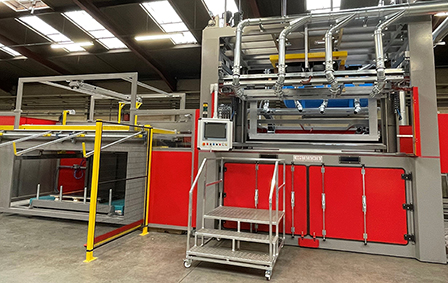
Preparation of the material
To offer its customers high quality products, GMI has invested in a large capacity oven which is used to prepare the thermoplastic before forming.
Machining
After thermoforming, the parts are sent to computer controlled 5-axes machining centres which are able to perform any type of machining or technical profiling combining precision, quality, repeatability and productivity.
Finishing
A finishing workshop completes installations and oversees controls and assembly: gluing, ultrasonic welding; marking – screen-printing- painting, riveting, assembly of accessories and insets…
Storage and logistics
The parts produced in our factories are stored in secure warehouses before shipping.
For products requiring regular, JIT transport, GMI oversees bespoke procurement logistics.
Recycling
GMI oversees the return and processing of thermoformed parts at end of life in its own recycling centre and issues a recycling certificate.